Как в Китае выпускают современные автомобили и батареи
В конце прошлого года китайский автопроизводитель Changan официально открыл один из самых передовых заводов в мировой автомобильной промышленности. Новое предприятие, расположенное в Чунцине, было построено всего за 352 дня и стало ключевым элементом стратегии компании по развитию электромобильного направления.
Масштабы и инвестиции
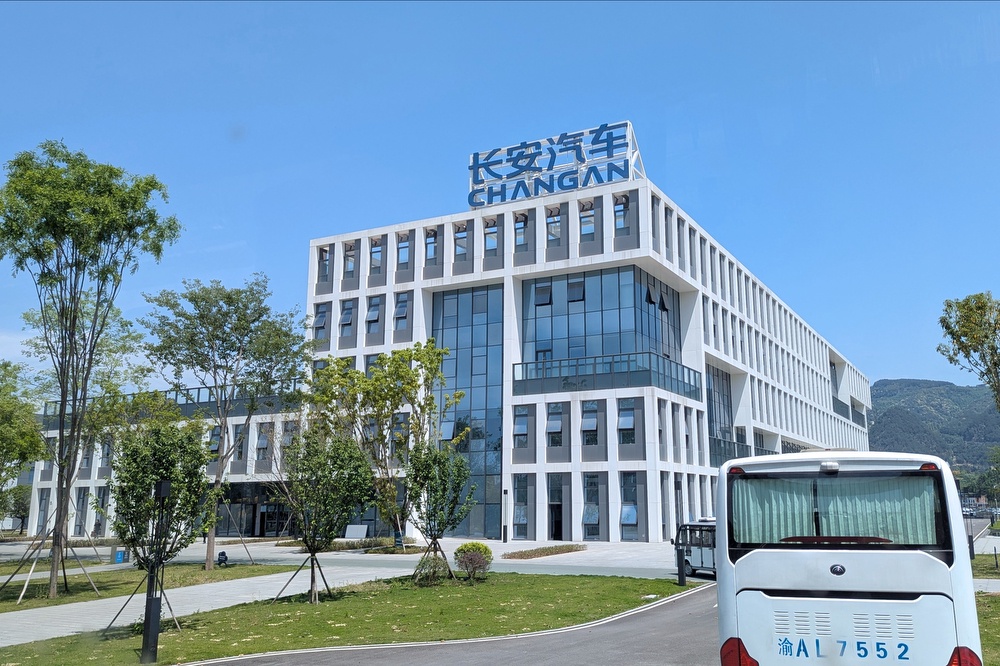
Строительство завода потребовало инвестиций в размере 10 миллиардов юаней (около 1,39 млрд долларов США). Производственная площадка занимает 77 гектаров и рассчитана на выпуск до 280 000 автомобилей в год. Основной упор делается на выпуск электромобилей, в частности, таких моделей, как Avatr 07, Deepal S05 и Changan Nevo E07.
Цифровая трансформация производства
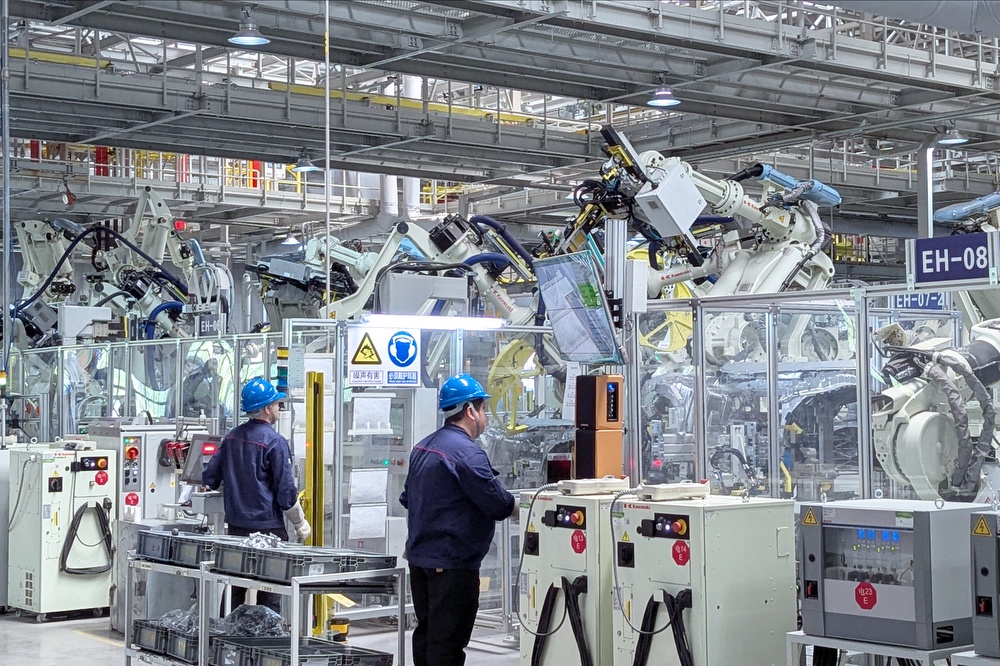
Новый завод воплощает концепцию "умного производства". Здесь установлено более 1 400 промышленных роботов, около 800 интеллектуальных производственных устройств и 650 автономных транспортных систем. Предприятие интегрировано в систему промышленного интернета нового поколения и использует технологии 5G и искусственный интеллект.
Цифровые двойники на каждом этапе производства позволяют моделировать процессы, прогнозировать отказы и оптимизировать логистику. Завод способен обрабатывать до миллиона точек данных в секунду, что обеспечивает точную и стабильную работу всех производственных линий.
Экологическая ответственность
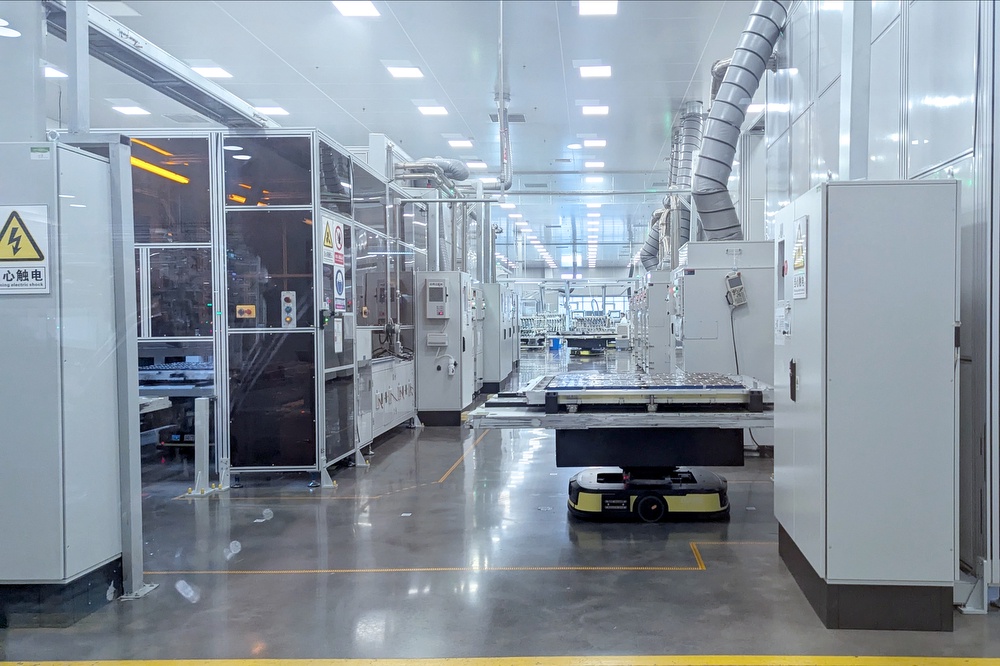
Одной из важных особенностей предприятия стала солнечная электростанция мощностью 36 МВт, установленная на крыше завода. По данным компании, она покрывает до 19% потребностей объекта в электроэнергии, снижая углеродный след и делая производство более безопасным для окружающей среды.
Новый этап для Changan и всего китайского автопрома
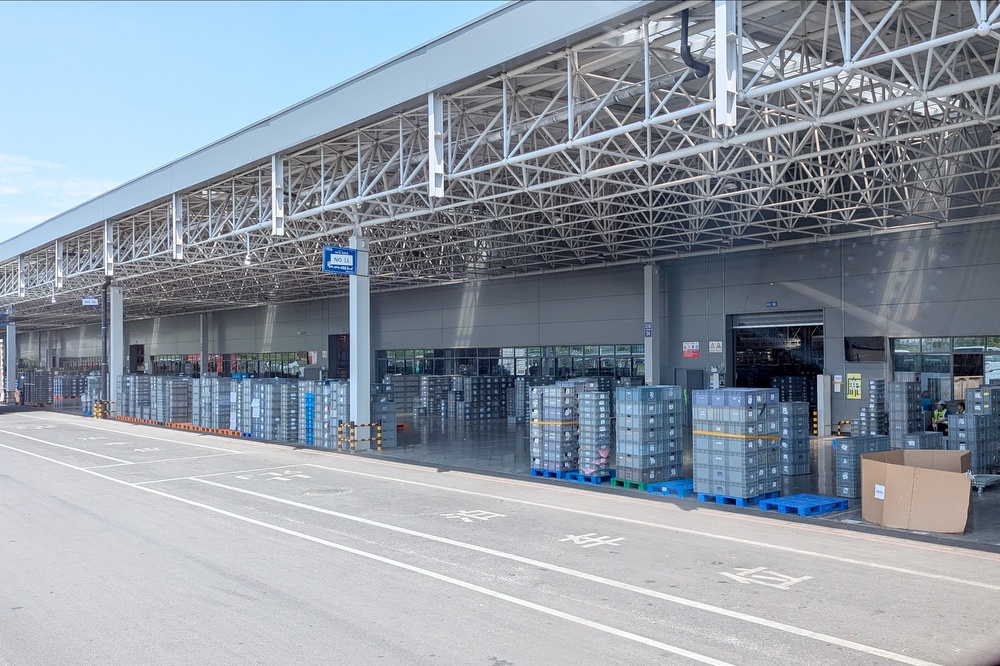
Changan активно трансформируется в глобального игрока на рынке новых энергетических транспортных средств (NEV). Открытие нового завода в Чунцине демонстрирует не только производственные амбиции бренда, но и общее направление развития китайской автомобильной отрасли - в сторону полной цифровизации, автоматизации и экологической устойчивости.
По масштабу, уровню автоматизации и технологической зрелости это предприятие уже сравнивают с лучшими заводами Tesla и Volkswagen. В ближайшее время завод станет центром серийного выпуска моделей нового поколения, рассчитанных как на внутренний рынок, так и на экспорт.
Когда говорят об автомобильной промышленности будущего, часто вспоминают электромобили, автопилот, цифровые экраны и мобильные приложения. Но всё это невозможно без того, что скрыто от глаз конечного потребителя - передовых производственных процессов, которые закладывают основу качества, безопасности и технологичности автомобиля. На заводе Changan нам удалось побывать в цехе сварки и цехе сборки батарей и своими глазами увидеть, как формируется "железная основа" современного автомобиля - от сварного кузова до высокотехнологичной батареи.
43 тысячи квадратных метров точности
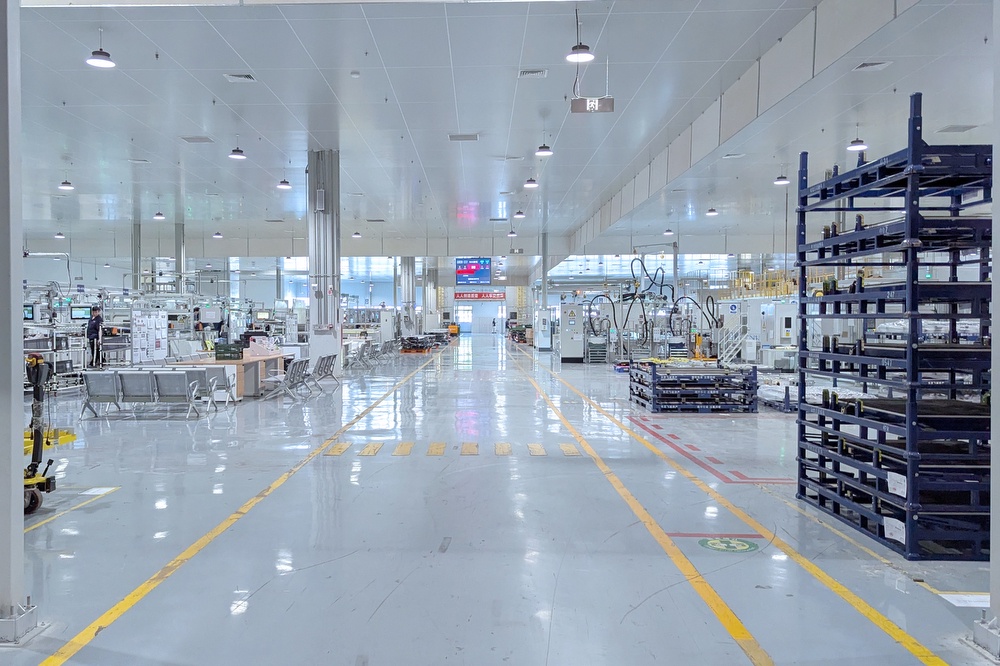
Сварочный цех завода Changan - это 43 000 м² высокотехнологичного пространства, где в буквальном смысле рождается кузов автомобиля. Сюда поступают листовые металлические детали, а на выходе - кузов в виде "сырца", готовый к покраске и дальнейшей сборке.
Автоматизация здесь на уровне 95%. Работают 471 робот и 185 сварочных постов, и всё это - с поразительной точностью и производительностью: одна из линий способна выпускать до 60 кузовов в час, обслуживая до 8 разных моделей.
Инженерная мысль особенно ярко проявляется в зоне сборки боковин: роботы-манипуляторы соединяют металлические детали, клеильные роботы герметизируют швы, а специальная система видеоинспекции в режиме реального времени следит за качеством нанесения клея. В итоге - максимальная точность без остановки производства.
Чтобы обеспечить безопасность при столкновениях, боковины кузова создаются методом горячей штамповки цельных деталей, что делает панели в 2-3 раза прочнее традиционных аналогов.
Самая гибкая линия
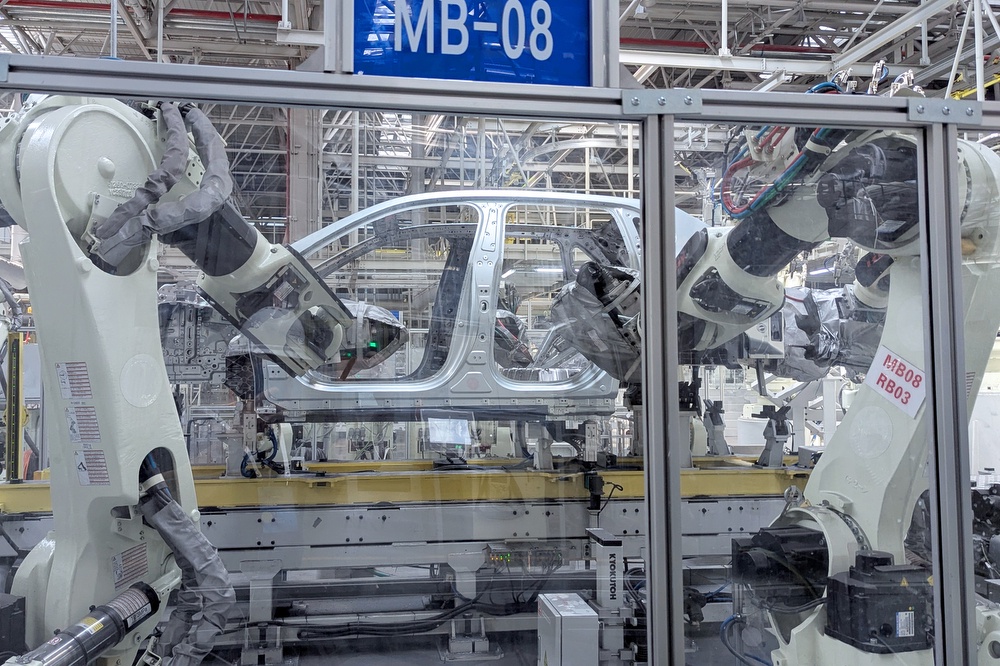
Главная гордость сварочного цеха - гибкая линия основной сборки кузова. Здесь 116 роботов и всего 26 рабочих станций, но благодаря сервоприводам и "умным" приспособлениям линия может моментально адаптироваться под выпуск разных моделей. Цикл сборки - всего 51 секунда.
На рабочих станциях MB-09 и MB-10 применяются уникальные методы соединения деталей: гидроформирование и самоклепание, позволяющие обойтись без пробивки отверстий и лишних отходов. Всё выглядит так, будто болт сам по себе соединяет панели, точно и без изъянов.
Дополняет всё это компактный, но мощный шлифовальный цех, работающий с защитным газом CO₂, и оснащённый автоматической системой уборки. Визуально особенно впечатляет автоматизированная сборка задних дверей: никаких зажимов, никакой ручной подгонки - всё делает техника.
Интеграция стали и алюминия
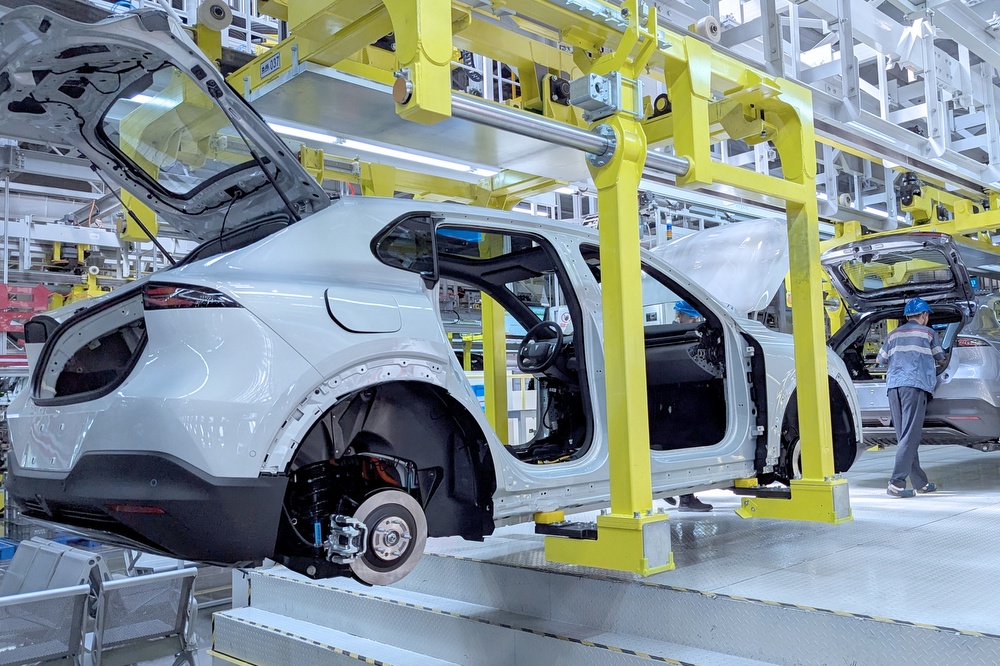
Отдельного внимания заслуживает линия сварки шасси, которая считается самой быстрой в Китае. В ней сочетаются технологии штамповки, стальной и алюминиевой сварки. Цельнолитые алюминиевые элементы заднего пола и моторного отсека объединяют 163 компонента всего в две детали. Результат - минус килограммы, плюс точность и производительность. По энергоёмкости и безопасности эта конструкция превосходит традиционные стальные аналоги на 54%.
Батарея как сердце электромобиля
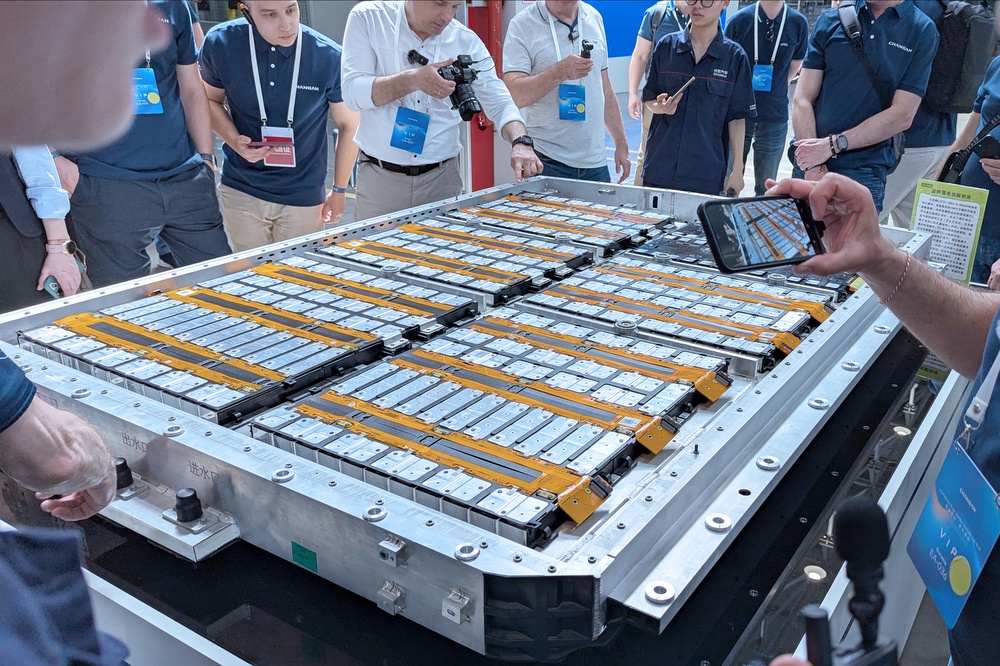
Если кузов - это скелет, то батарея - сердце электромобиля. И в этом смысле цех по производству батарей Changan заслуживает отдельной главы. Его площадь - 39 000 м², и это один из самых современных и масштабных объектов в отрасли.
Производительность поражает: одна батарея - каждые 60 секунд. В сутки - продукция на миллиард юаней. План - 280 000 батарей в год. В штате - всего 100 человек, но с таким уровнем автоматизации этого более чем достаточно.
Процесс разделён на два этапа: предварительная и финальная сборка. На первом - 85 роботов, 235 единиц оборудования и 120 транспортных систем работают в полной автономии, собирая модули из отдельных элементов. Эти элементы производятся по собственной технологии Changan, с особым контролем качества.
Используются популярные составы - LFP и NCA, но с внутренней оптимизацией, благодаря которой батареи заряжаются быстрее, а запас хода после 15 минут зарядки достигает 365 км. Это и есть "Золотая броня" - флагманская батарея компании.
Внутри - высокоточные процессы
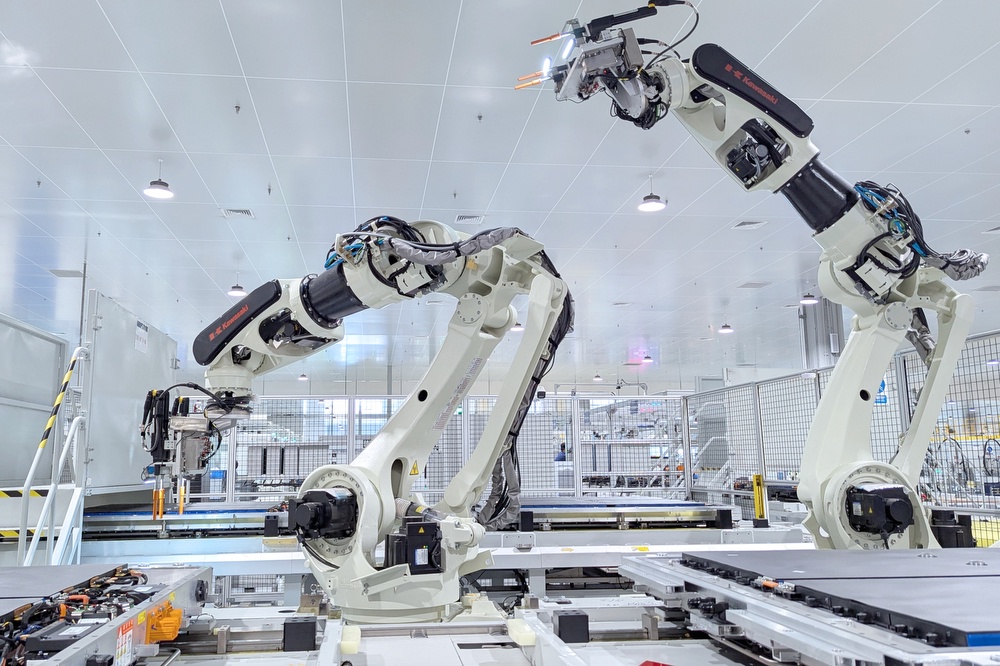
Контроль качества здесь на высшем уровне. Камеры Hikvision следят за каждым этапом, а лазерная и плазменная очистка обеспечивают идеальную чистоту элементов. В зоне сборки батарейных блоков всё организовано по U-образной логике, исключающей необходимость в погрузчиках - минимум рисков, максимум эффективности. А вот в сборке медных шин, по сути, это "токовые артерии" батареи, работают настоящие мастера: автоматические зажимы Atlas, визуальное позиционирование и полная защита от короткого замыкания.
Итог
Завод Changan - это не просто "конвейер" по производству машин. Это демонстрация того, как современные технологии, инженерия и автоматизация переплетаются в симфонию эффективности. В каждом кузове, в каждой батарее чувствуется подход, где важна не только скорость, но и точность, безопасность, гибкость и забота о будущем.
Производство как искусство - так можно описать увиденное.